For the past 30 years, Hanwha Solutions Chemical Division R&D Center has been committed to developing and applying cutting-edge technology. We have led the advancement of chemistry in South Korea with the vision of creating a more prosperous future for humanity. To this end, we have conducted research into next-generation technologies and materials that can drive the new future. Our R&D investments are allowing us to develop eco-friendly and value-added products in the polyolefin and chemical markets. At the same time, we’re adopting innovative measures that translate to cost reductions and process improvements that further strengthen our business competitiveness.
Hanwha Solutions Chemical Division R&D Center is continuing to seek change as a global industry leader through new technologies that set new standards. We’re driving change for life, for the better.
- Securing future growth engines Our R&D strategy is part of a bold enterprise-wide roadmap to develop original technologies. These new technologies will give rise to new products for new businesses.
- Strengthening existing competencies To secure our leadership positions in each of our businesses, we’re expanding our value-added product portfolios, aggressively using research to advance conventional processes, improving product quality, and reducing cost.
- Creating a pool of experts We are promoting a creative environment and investing in diverse programs to nurture talents who will pursue advanced research in teams made up of other exceptional individuals and SMEs.
- Building a global R&D network We are partnering with global technology leaders and prominent research institutions to develop original and emerging core technologies that will drive our leadership in the global market.
R&D Organization
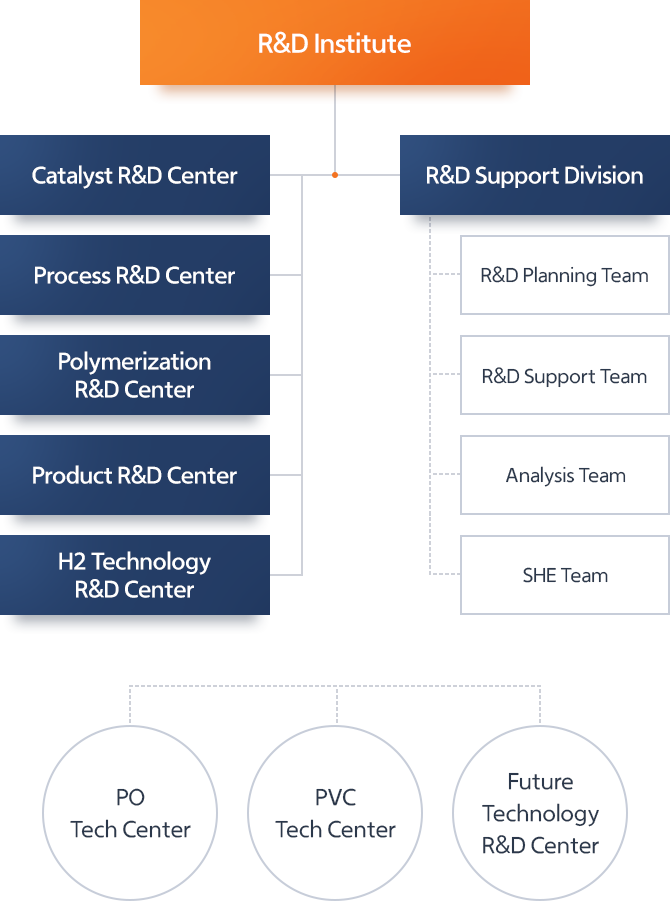
R&D Insitute
- Catalyst R&D Center
- Process R&D Center
- Polymerization R&D Center
- Product R&D Center
- H2 Technology R&D Center
- R&D Support Division
- R&D Planning Team
- R&D Support Team
- Analysis Team
- SHE Team
- PO Tech Center
- PVC Tech Center
- Future Technology R&D Center
R&D History
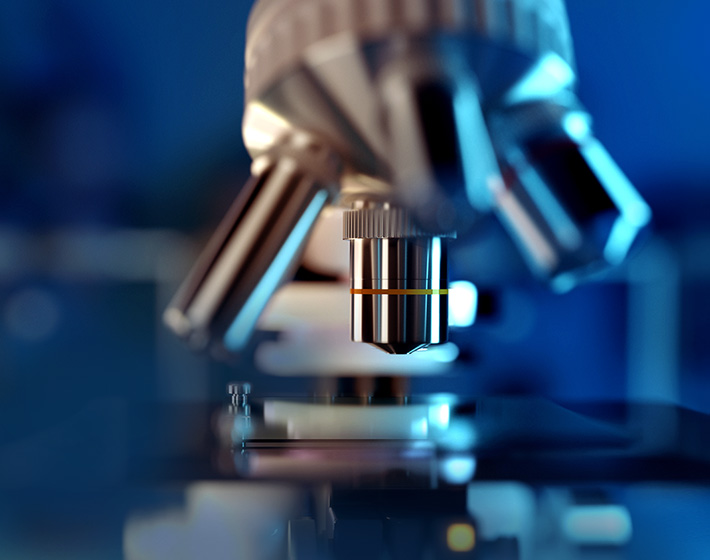
- 1979 Daedeok R&D Center is established
- 1985 First company in Korea to develop XLPE for electric cable insulation
- 1991 First company in Korea to develop XLPE for EHV power cable insulation
- 1996 High-content EVA used in shoe soles is successfully developed
- 2002 Proprietary ASR is successfully developed
- 2003 OEM technology for ultra-high-content EVA is secured
- 2008 DOTP plasticizer is successfully developed
- 2011 LLDPE for cable project is awarded Best Government R&D Project
- 2012 HDPE for film & injection molding is commercialized
Eco-friendly plasticizer is successfully developed - 2014 Acquires New Excellent Technology (NET) certification for eco-friendly plasticizer (DEHCH)
- 2015 Develops XLPE for HVDC power cable insulation
- 2016 Acquires New Excellent Technology (NET) certification for high value CPVC and metallocene catalyst
- 2017 Commercializes in-house technologies on high value CPVC and eco-friendly plasticizer (DEHCH)
Acquires New Excellent Technology (NET) certification for high purity XDI - 2018 Wins IR52 Jang Young-Shil Award for eco-friendly plasticizer (DEHCH
- 2019 Acquires New Excellent Technology (NET) certification for and commercializes in-house technology of H-HCR (Hydrogenated Hydrocarbon Resin)
Wins IR52 Jang Young-Shil Award for high value CPVC - 2020 Commercializes in-house technology on high purity XDI
Commercializes in-house technology on PVC large-scale reactors - 2021 Jang Young-sil Award for H-HCR (Hydrogenated HydroCarbon Resin) IR52
- 2022 Certified as the World-Class Product of Korea(Eco-DEHCH, PVC, CP/TP)
Acquires New Excellent Technology (NET) certification for Semicon with EBA - 2023 Acquired Global Recycled Standard Certification for rPE
- 2024 Jang Young-sil Awards for Semi-conductive compound
Key Research Areas
-
- Olefin Polymer
- Main areas of research: Ethylene Homo/Co polymer(LD, LLD, HD, m-LLD, EVA, W&C etc.)
- Our research on diverse olefin products (EVA, LDPE, LLD/HDPE, metallocene PE, W&C compound) is part of our endless pursuit to satisfy customer needs – one of which is to lead with specialty products that possess greater durability and processability.
-
- PVC / Specialty PVC
- Main areas of research: PVC, Paste, CP/TP, CPVC
- Our research on multiple grades of PVC formulation and production processes will further strengthen our business competitiveness. And to expand our portfolio of highly functional specialty products that yield greater profit margins, we’re heavily investing in R&D on copolymer, terpolymer and CPVC.
-
- Catalyst
- Main areas of research: Metallocene Catalyst, Ziegler-Natta Catalyst, Petrochemical Catalyst
- Our research on developing metallocene and Ziegler-Natta catalysts reflect our efforts to secure original technologies and at the same time develop high-value-added specialty PE products. Our research into petrochemical catalyst is part of our strategy to diversify our product portfolio and become further competitive in the market.
-
- Petrochemical Process
- Main areas of research: Manufacturing processes for petroleum resin, eco-friendly plasticizers, isocyanates, intermediates for new products, energy-saving separation process, and PE polymerization process
- We believe research on process development is essential for commercializing new processes. Research is also a means to our goal: to reduce production costs and impact to the environment. We work to optimize process designs and develop energy-saving reaction/separation process technologies by using computer simulations to create concept designs for new processes that are both more efficient and effective.
-
- Eco-friendly Plasticizer
- Main areas of research: Eco-DEHCH
- We continuously monitor market trends in eco-friendly products and customer needs. We factor our learnings into research to improve our development of general-purpose eco-friendly plasticizers and plasticizers with specialized functions. One example of a product that has been the result of our R&D efforts is the Eco-DEHCH, an eco-friendly plasticizer with a remarkable improvement in stability and processability. Eco-DEHCH, developed with our proprietary technology, has been well-received by customers and as a result, commercially successful.
-
- Functional Polymer
- Main areas of research: DCPD petroleum resin, high-performance adhesive resin, alkali soluble resin
- We are developing polymers that exhibit an adhesive quality when added to products and can be applied to diverse functional adhesives, tapes, hygienic products, food packaging, printing ink, surface protection coating, paint, etc. Main products under development are functional polymers, such as hydrogenated petroleum resin, an ingredient in adhesives used in hygienic products and food packaging.
-
- Research on Isocyanate
- XDI (m-xylylene diisocyanate)
- Specialty Isocyanate and its derivatives and applied products are being researched. We are the first company to have completed the development of XDI with our proprietary technology and have succeeded in its commercialization in 2020. XDI is a high-value added material that has excellent optical properties, being highly refractive and does not turn yellow. It is a specialty chemical material used in optical lenses, adhesives, ink binders, coatings, etc.
-
- Research on super engineering plastic
- PEKK, Polyetherketoneketone
- As an effort to secure our future growth engine and business diversification, we are developing super engineering plastic materials. Key products developed so far include PEKK polymers and compound materials used in semiconductors, electrical and electronic products, industrial, aviation, and medical usages.
-
- Research on Anion exchange membrane (AEM)
- Water electrolyzers
- We are developing the manufacturing technology of hydrogen, which is a carrier of clean energy that can replace fossil fuels. In particular, our goal is to manufacture green hydrogen using renewable energy, by developing and commercializing the AEM water electrolyzers. We are developing not only the parts, such as the AEM and the catalyst, but also a smart system that allows renewable energy fluctuation of load. AI and machine learning is introduced in all aspects, allowing for data based, advanced, scientific, and systematic research.
-
- Research on PTC
- Plastics-to-Chemicals
- We are doing research on Plastics-to-Chemicals (PTC), where waste plastic can be recycled back to become a petrochemical base material. By degrading waste plastic in high temperature, pyrolysis oil is extracted, which in turn is transformed to naphta under high temperature and high pressure. We are working on the transformation of a double bond into a single bond, removal of impurities, and developing a catalyst and process for adjusting the molecular weight.
R&D Achievements
-
High-content EVA
- Overview
-
- Elastromeric polymer with VA content of 40% developed with autoclave technology
- Used to produce HMA (Glue), Running Shoes, and Ink
- Properties
- High transparency, elasticity, and adhesiveness. As a holt melt adhesive, it is used in adhesive products such as glue sticks and plastic wraps. As foam, it is used in sporting equipment such sports shoes padding, gloves and helmets.
- Key achievements
- In 2004 became Korea’s only petrochemical manufacturer to succeed in commercializing EVA with 40% VA
-
Ultra-high-voltage Cable (XLPE)
- Overview
- Cross linked PE for cable insulation
- Properties
- Smoother surfaces and Clean Technology that reduces CPVs (contamination, protusions, or voids) resulting in better insulating and electrical properties, longer cable life, and reduced impact to the environment
- Key achievements
-
- Replaced import-dependent insulation material with Hanwha’s domestically produced XLPE
- Awarded numerous domestic and international certificates for Hanwha’s XLPE insulated cables
- Selected as world-class product of Korea every year since 2008
-
Eco-DEHCH
- Overview
- Highly functional non-phthalate eco-friendly plasticizer
- Properties
-
- Superb as plasticizer due to low viscosity and translocation property
- Perfect as non-phthalate eco-friendly plasticizer
- Key achievements
-
- Received 2014 NET certification from Korean Government
- Completed construction of commercial plant through proprietary technology (2017)
- Gained FDA approval for products containing Eco-DEHCH
- REACH (Registration, Evaluation, Authorization and Restriction of Chemicals) implemented in 2013.
-
CPVC
- Overview
- CPVC resin was manufactured using fundamental PVC morphology control technology and optimized chlorinated reaction
- Properties
- More heat and chemical resistant than PVC and easier to use than steel pipes. CPVC is used manufacture sprinklers, industrial pipes, and hot water pipes
- Key achievements
-
- Received the 2016 NET certification from Korean Government
- CPVC is commercialized for the first time in Korea in 2017
-
Metallocene hybrid catalyst
- Overview
- Metallocene hybrid catalyst technology for gas-phase process can be used to produce MD/HDPE with excellent mechanical properties and processability
- Properties
- Controls polymer structure to provide long-term hydrostatic strength, improve stress crack resistance, and increase processability
- Key achievements
-
- Production of PE-RT TYPE Ⅱ using Hanwha Solutions Chemical Division’s Metallocene hybrid catalyst technology was certified by the international accreditation agency EXOVA in 2017
- Acquired New Excellent Technology(NET) certification from Korean Government in 2016
-
PE-RT
- Overview
- PE-RT(Polyethylene of Raised Temperature Resistance) TYPE Ⅰ/Ⅱ is a polyethylene resin whose molecular structure allows it to operate at elevated temperatures and therefore most commonly used in eco-friendly hot-water pressure pipes made of plastic.
- Properties
- Leveraging technologies such as hybrid catalyst technology, PE-RT features long-term hydrostatic strength, chemical resistance, resistance to stress crack and high processability.
- Key achievements
- Acquired quality certification for PE-RT TYPE Ⅰ/Ⅱ from EXOVA in 2016 and 2017
-
DCPD hydrogenated petroleum
- Overview
- Non-toxic, high-quality hydrogenated petroleum resin
- Properties
-
- Highly transparent, colorless, and odorless polymer resin
- Non-toxic and especially suited for high-quality binding in hygienic products, food, and medical use
- Key achievements
-
- Independently developed high-temperature polymerization and high-pressure hydrogenation processes
- Developed high-transparent, colorless and odorless products
- Plant to engineer products using proprietary technology currently under construction
-
XDI (m-xylylene diisocyanate)
- Overview
- Develop high purity XDI with excellent optical properties
- Properties
-
- Does not turn yellow, high reaction speed, highly refractive. Has merits of both aromatic and aliphatic isocyanate.
- With excellent optical properties, is used in making highly refractive optical lenses (refractive index 1.67)
- Key achievements
-
- 2017 Acquires New Excellent Technology (NET) certification for high purity XDI
- 2020 Selected as Industrial Technology Achievement 2020 from The National Academy of Engineering of Korea
- 2020 Built commercialization plant with proprietary technology
-
PEKK, Polyetherketoneketone
- Overview
- Develop PEKK material, which is a super engineering plastic. It has the highest level of high heat, chemical, and mechanical load resistance among thermoplasticity polymers.
- Properties
-
- Has excellent mechanical load, high heat, chemical, fire resistance, as well as excellent self-lubricative and biocompatibility properties. Has a wide range of usage from semiconductors
- Display process, automobile parts, aviation mechatronics
- Parts, electrical and electronic material, to medical implants.
- Key achievements
-
- In-house development of high polymerization technology and process
- Have been selected to participate in a national project to verify the technology and develop applied products
-
Anion exchange membrane
- Overview
- Develop AEM water electrolyzers that can connect to renewable energy
- Properties
-
- High-performing, highly durable, low-cost AEM Water Electrolysis system
- Can respond rapidly to renewable energy’s fluctuation of load
- AI based optimized system operation
- Key achievements
-
- Developed a proprietary AEM Water Electrolysis system
- Participate in a national project for highly safe alkaline water electrolyzers
-
Plastics-to-Chemicals
- Overview
- Develop technology for naphta producing hydrogenation catalyst/process that are pyrolysis oil based
- Properties
-
- By having the same physical properties with the existing naphta, PTC can be used to make recycled product that are identical to the virgin plastic product
- Also can be used as material for food and medical packaging plastic, which until now are not permitted to use recycled plastic.
- Contributing to the realization of plastic circular economy and carbon neutrality
- Key achievements
- Joint research with Korea Institute of Energy Research, national project in progress